The Aluminum Die Casting Process
Aluminum die casting is a manufacturing process that produces accurately, defined, smooth and textured-surfaced metal parts.
The casting process applys a steel mold often capable of producing tens of thousands of casting parts in rapid succession, and requires the fabrication of a mold tool–called a die–that can have one or multiple cavities. The die must be made in at least two sections to permit removal of castings. Molten aluminum is injected into the die cavity where it solidifies quickly. These sections are mounted securely in a machine and are arranged so that one is stationary while the other is moveable. The die halves are drawn apart and the casting is ejected. Die casting dies can be simple or complex, having moveable slides, cores, or other sections depending on the complexity of the casting. Low-density aluminum metals are essential to the die casting industry. The Aluminum Die Casting process retains a durable strength at very high temperatures, requiring the use of cold chamber machines.
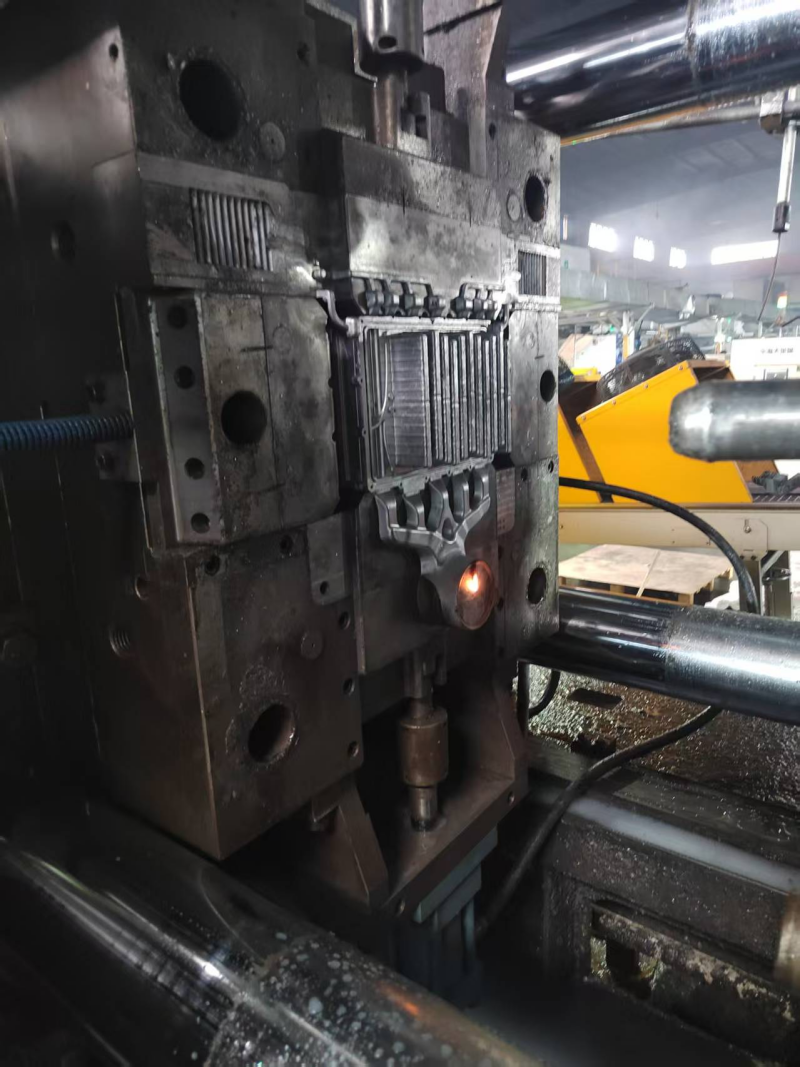
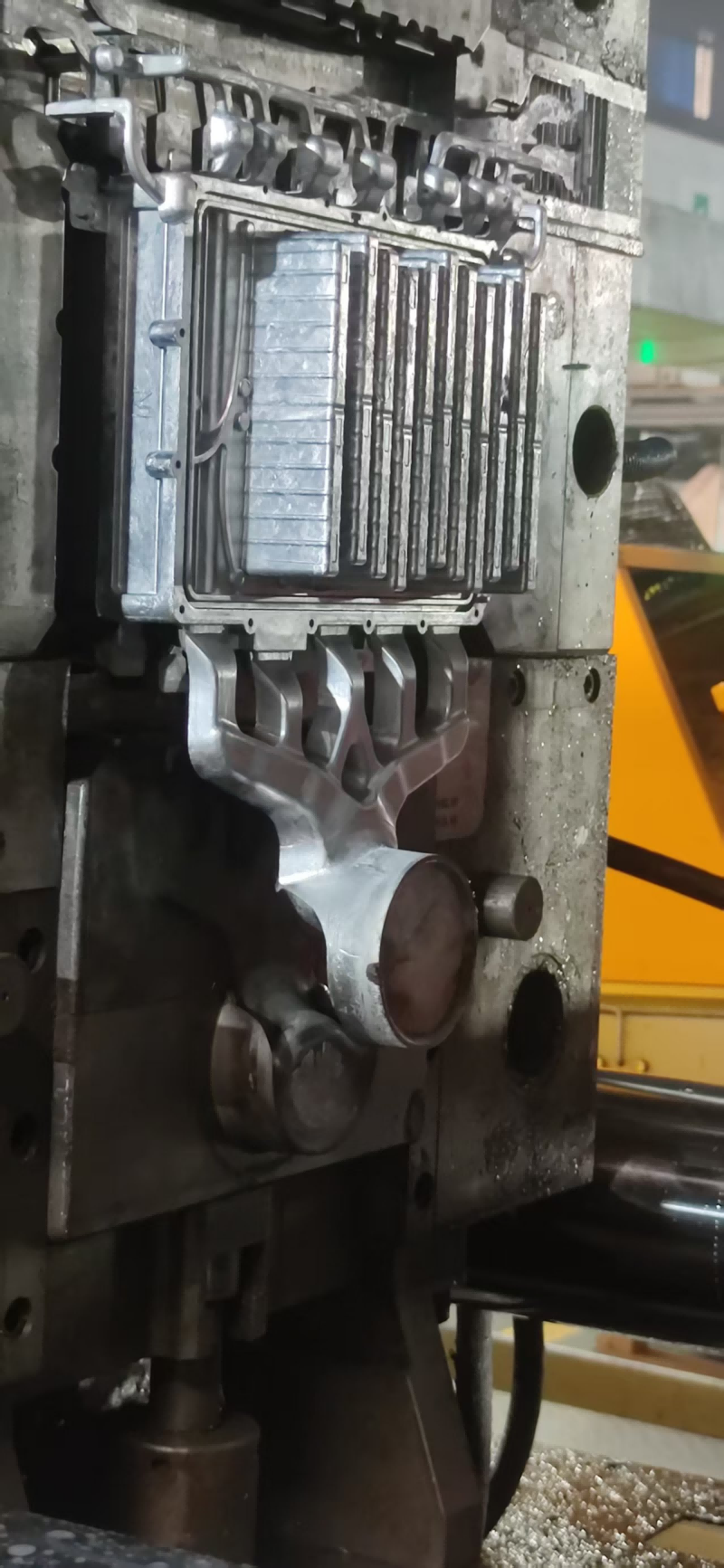
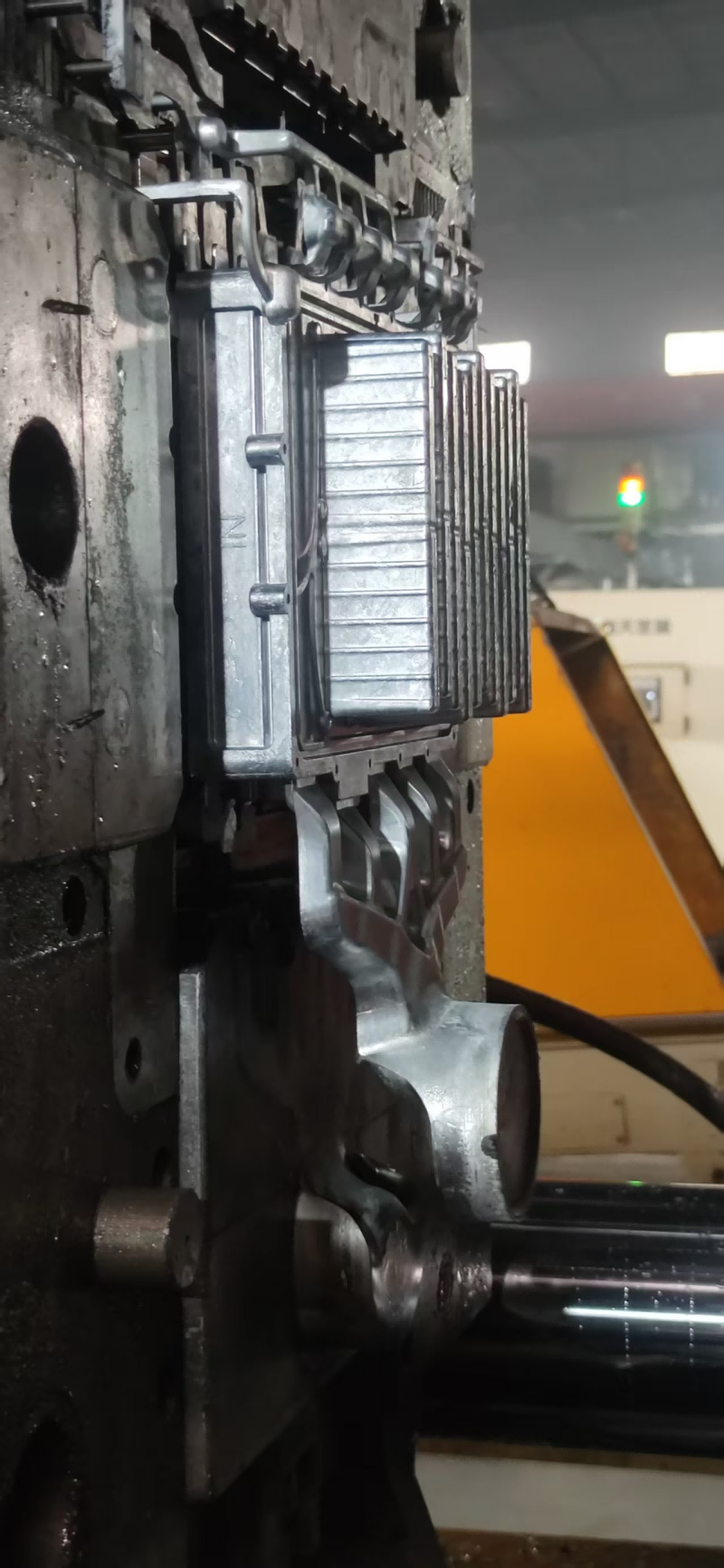
The Advantages of Aluminum Die Casting
Aluminum is the most commonly cast non-ferrous metal in the world. As a lightweight metal, the most popular reason for utilizing aluminum die casting is that it creates very lightweight parts without sacrificing strength. Aluminum die cast parts also have more surface finishing options and can withstand higher operating temperatures than other non-ferrous materials. Aluminum die cast parts are corrosion resistant, highly conductive, have a good stiffness and strength-to-weight ratio. The aluminum die casting process is based on rapid production that allows a high volume of die casting parts to be produced very quickly and more cost-effectively than alternative casting processes. Characteristics and Advantages of Aluminum Die Castings include:
● Lightweight and Durable
● High dimensional stability
● Good Stiffness and Strength-to-Weight Ratio
● Good corrosion resistance
● High thermal and electrical conductivity
● Fully Recyclable and Reusable in Production
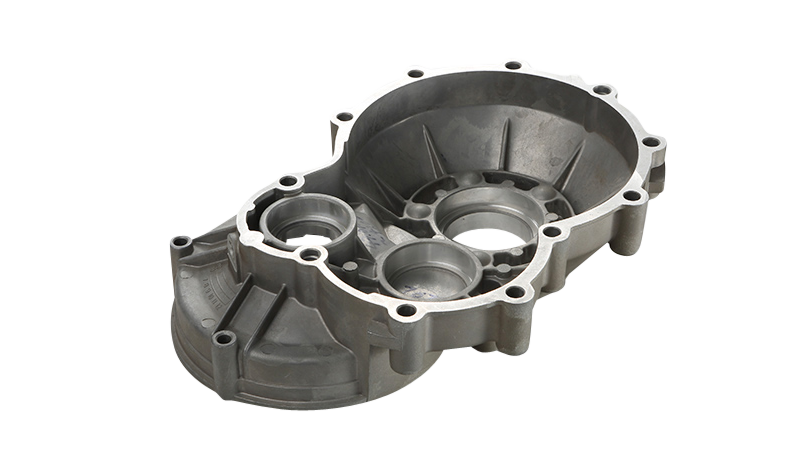
Clients can choose from a wide range of alloys for their aluminum die cast components. Our common aluminum alloys include:
● A360
● A380
● A383
● ADC12
● A413
● A356
A Reliable Aluminum Die Casting Manufacturer
● From design concept to production and delivery, you only need to tell us your requirements. Our expert service team and manufacturing team will complete your order efficiently and perfectly, and deliver it to you as quickly as possible.
● With our ISO 9001 registration and IATF 16949 certification, Kingrun meets your exact specifications using state-of-the- art equipment, a strong management team, and a highly skilled, stable workforce.
● 10 sets die casting machines range in size from 280 tons to 1,650 tons producing aluminum die casting components for low and high volume production programs.
● Kingrun can provide CNC prototyping service if customer wants to test samples before mass production .
● Various products can be diecast in the factory : Aluminum alloy Pumps, Housings, Bases and Covers, Shells, Handles, Brackets etc.
● Kingrun helps to solve problems. Our clients value our ability to turn complex design specifications into reality.
● Kingrun handles all aspects of aluminum die cast manufacturing, from mold design and testing to aluminum parts manufacturing, finishing, and packaging.
● Kingrun completes some surface finishings to ensure parts meet specifications in both a timely and cost-effective manner, including deburring, degreasing, shot blasting, conversion coating, powder coating, wet paint.
Industries Kingrun Served:
Automotive
Aerospace
Marine
Communications
Electronics
Lighting
Medical
Military
Pump Products